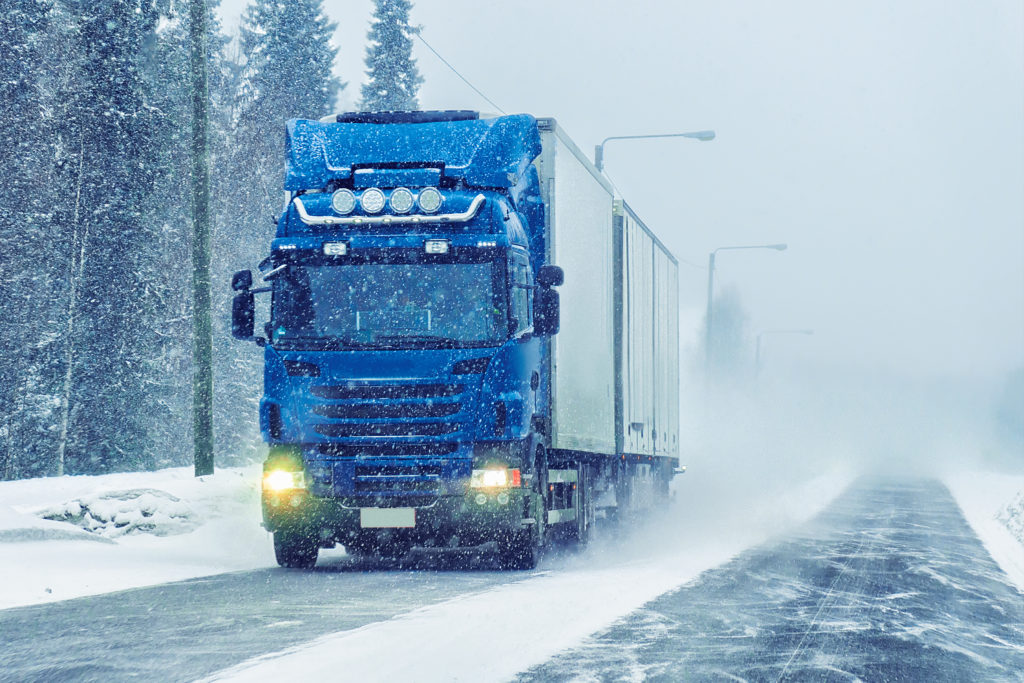
As the leaves begin to fall, it is the time of year where transportation managers shift their focus away from hurricane readiness and toward polar vortex preparedness. Before it is cold outside, make sure our diesel fuel is ready for what lies ahead.
1. Check your tank conditions.
Take a sample of fuel from your diesel tank using a bottom sample kit. The sample should be sent to a laboratory to test for the presence of microbial growth or water. Microbes love diesel. Moisture helps them grow. This love affair can create havoc during the cold. You want to address these conditions before winter. The lab results will tell you if a biocide or water dispersant treatment are needed.
2. Change your filters.
You should change the filters on your trucks to 20 microns or higher and filter only for particulates. The filter on your fuel dispenser should be 30 microns or higher and filter only for particulates. Complaints about diesel gelling are often traced back to frozen debris in filters that have not been changed since the Clinton administration. Change your filters and avoid a common cause of winter fuel frustration.
3. Take nozzle samples throughout winter.
The Cloud Point (CP) of diesel is the temperature where wax becomes evident and problems begin. The source of crude used to make your diesel influences your diesel’s CP. The type of biofuel added to your diesel impacts your diesel’s CP. As a result, some regional diesel fuels do not respond well to fuel treatments. The only way to know for sure if your winter plan is effective is by sending a fuel sample to the lab to measure the CP of your diesel. Your local refinery may change crude sources or biofuel components during the winter season so test periodically. A nozzle kit with three samples costs less than one hour of a driver and a revenue bearing asset sitting idle. Be smart. Take periodic nozzle samples.
4. Adjust treatment approaches as needed.
As a general rule, untreated fuel in the US starts to gel at 15֯ F. Much of the US needs their fuel to perform well below that temperature to keep their trucks moving. There are two common ways to achieve this.
The most common method is a No1 diesel blend (70% No2 and 30% No1 as an example). Adding No1 diesel to your No2 will lower your CP. While No1 diesel helps your winter operability, it does come with concerns. First, No1 diesel is not cheap. Prices for No1 can be as high as $.75 per gallon more than No2. Second, No1 can have limited availability in certain markets. Lastly, excessive blends of No1 will have a negative impact on your diesel engine’s performance.
An alternative to a No1 blend is to use a winter fuel treatment. Fuel treatments can be much more cost effective than No1 blends, but their effectiveness may vary by region (See Step #3).
You will know if your plan hits the target temperature with the nozzle sample lab results. If your target CP temperature is -25֯ F and your lab results show only -10֯ F, then you need to adjust your treatment strategy. Limit reliance on No1 if you can. Tweak as needed.
5. Prepare for the worst
The phrase “Polar Vortex” seems to have come into vogue in recent winters. This weather phenomenon means extreme colds that could be well below the temperature you carefully targeted. Also, if you are buying fuel at retail stations then you lose some control over the CP targets. Keep an emergency treatment on hand just in case your well laid winter plan is thwarted by mother nature or a penny-pinching fuel station.
6. Know when to ask for help
If you need help with any of these steps in your winter fuel strategy, can contact us at Info@Diversified.Energy. We provide the Fuel Treatments you need and can help you prepare a plan that minimizes costs and maximizes effectiveness.